On the safe side – with a comprehensive quality assurance system
Our company uses a medical device quality assurance management system in accordance with EN ISO 13485 and fulfils all additional requirements stipulated by this guideline and ensures that our products are fully compliant.
Our commitment: For a healthy society and your legal protection.
Medical devices are products that are used for a medical purpose, such as diagnostics treatment or alleviation of disease (e.g., as per SBG IX). These include ultrasound devices, endoscopes, implants, and training devices for treatment and rehabilitation, which are all tested for their accuracy, technical and biological safety, effectiveness, and intuitive usability. All these products meet the most stringent requirements.
The requirements are incredibly high. Within the framework of a certified quality management system, in accordance with EN ISO 13485:2021, and the European Union regulation EU 2017/745 on Medical Devices, all stages of planning, development, and production are systematically planned implemented, verified, and validated by a team of highly qualified and motivated experts and in line with international standards.
During annual audits, an independent entity (e.g., TÜV) examines and assesses adherence to the required quality standard.
The type plate of each device must display the CE marking. For products with measurement technology or electronic control elements, the four-digit identification number of a notified body must be displayed after the CE marking (e.g., TÜV Süd – CE 0123).
The device manufacturer, or device supplier, is also obligated to provide a declaration of compliance for each product on request. Every facility operator should have this declaration on hand at their facility to avoid possible legal consequences resulting from enquiries by the responsible state authority.
Yes, the risks can be significant. If a physician, therapist or operator uses an unapproved medical device for medical purposes (e.g., physiotherapy using modalities) and a patient is harmed, this may be considered negligence and be subject to the corresponding legal consequences.
Non-medical devices that are used as medical devices are defined by law as medical devices and must fulfil all respective requirements applied to medical devices.
A medicine ball is also a medical training device - precisely when it is used on the patient. Just like the medicine ball, many medical training devices are not sufficiently secured for therapy.
Medical products are completely different: they have tested technical, clinical and biological safety features. For the safety of patients and operators.
Training equipment approved for medical use has
- Proven clinical effectiveness
- Full risk management
- Certified biological, electrical, and mechanical safety
The products also continue to undergo permanent technical and clinical monitoring while in use to help reduce risks and ensure the success of the treatment - for a lifetime.
Medical devices undergo regular safety and/or measurement technology inspections or tests defined by the manufacturer. Proof of inspection or testing must be provided to the State Department for Social Services upon request.
By entering into a maintenance contract, regular inspections can be carried out automatically and documented without gaps.
Please note, connecting one of our medical devices to accessories or training controls not authorised by us can result in the product no longer being compliant with full risk liability is automatically transferred to the operator.
Modifications to devices at the customer's premises, for example the installation of third-party software or the attachment of a different display to a device that has already been delivered, must be authorised in writing by the manufacturer in advance, otherwise this device will lose its tested safety! This would mean that the operator would be fully liable for any damage or injury and the warranty and guarantee would be invalidated.
For the last 30 years, customers across the world have placed their trust in our medical testing and training systems and supported our vision for a healthy society.
With us, you are always on the safe side. We are a leading EN ISO 13485 and TÜV-certified medical device company that adheres to the most stringent safety and quality standards. All of our products meet the European Medical Device Directive (MDD) and the German Medical Devices Act (MPG) and display the CE marking.
As a certified company, we assign our products a service life, during which - after being brought into service – patient and operator are not at risk. During the service life, the manufacturer is obligated to provide spare parts for all repairs, because only spare parts supplied by the manufacturer in accordance with the design and risk management of the product can be used. We carry out the required market observation, which must also be guaranteed during the service life of the product.
During the entire product life cycle of a medical device, the possibility of discontinuation must be taken into account. We aim to provide our customers with long-term and professional product support – using our traffic light system. We use this system for both our own products and our retail products.
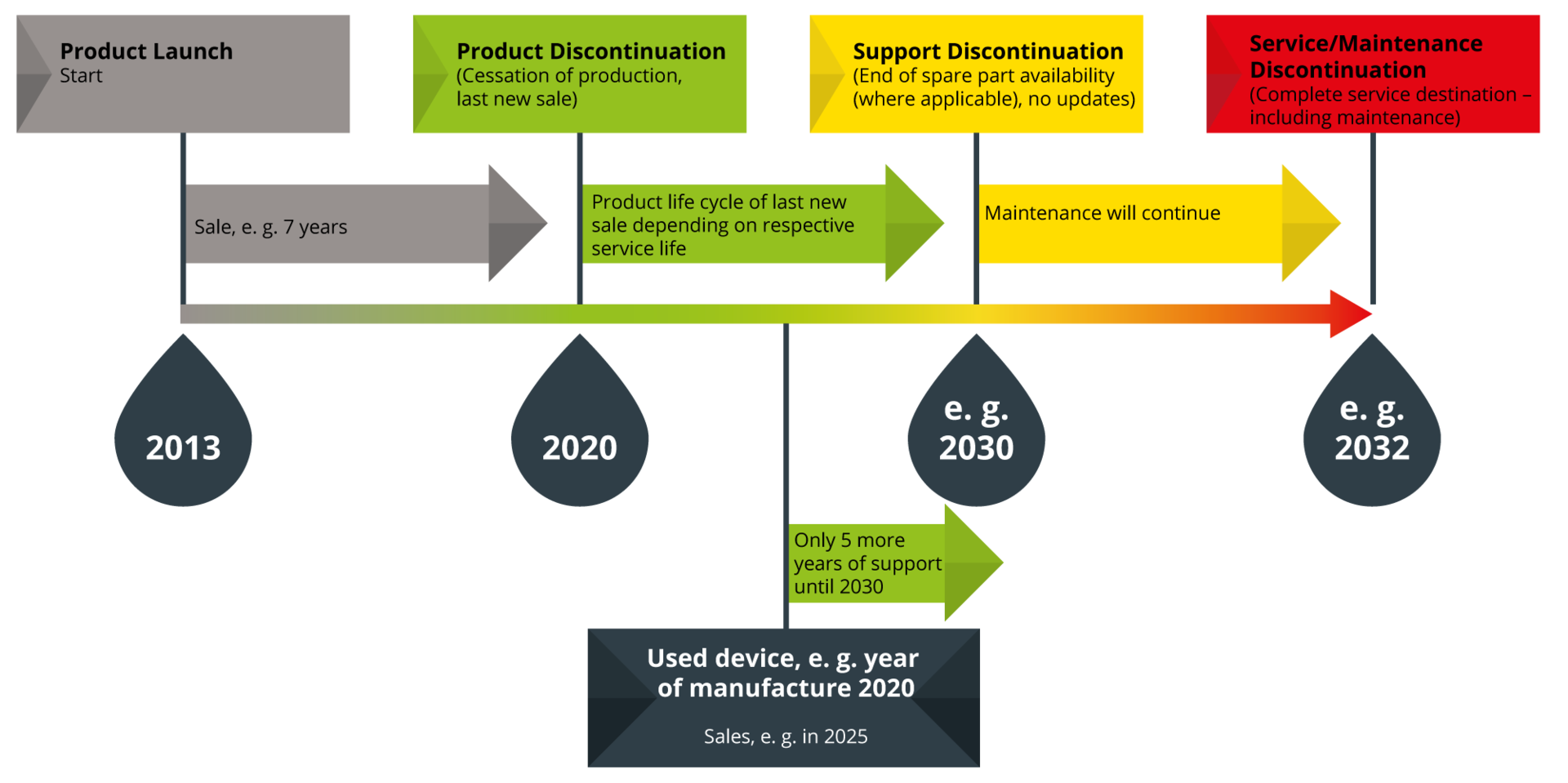
Explanation: For example, you purchase a used device in 2025, year of manufacture 2020. As per the product life cycle in our traffic light system, support will be provided for this device until 2030, until support for this device is discontinued.
- The product is no longer produced, no further new sales.
- The product remains subject to support service, spare parts will remain available at least until the end of the product service life.
- Maintenance continues as normal.
- The product can continue to be upgraded via updates/major updates.
- Retail products: The manufacturer discontinues the product, it is taken over by proxomed on their behalf, or the retail product is no longer sold via proxomed and the customer is referred to the manufacturer.
- The service life of the last product sold has come to an end.
- There are no, or only limited, spare parts available.
- Maintenance can continue. Note: Attempts will be made to preserve the functionality of the system, despite its age and potential wear-and-tear caused by hidden mechanical and electrical defects.
- The product is no longer upgraded via updates/major updates (with the exception of security updates).
- For example, the product has technical defects (e.g., covers break when removed), or the product no longer corresponds to the current state of development.
- There are no longer qualified technicians available who are trained to carry out maintenance in accordance with MPG.
- Maintenance is no longer carried out.
- The product is no longer upgraded via updates/major updates.